UT researchers, Volkswagen engineers and their collaborators created a liftgate made of a novel composite for the Volkswagen Atlas, which is manufactured in Chattanooga. The new liftgate reduces weight by 35 percent as well as lowers the company’s investment cost.
Volkswagen can produce high volumes of the liftgate quickly while producing lower amounts of waste and increasing the recyclability of the manufactured parts. The lighter weight helps increase fuel efficiency for the vehicle.
UT led the way in this game-changing innovation project working with Volkswagen engineers, Oak Ridge National Laboratory researchers and other academic partners. Students also contributed to the project, learning skills that will help them far beyond the classroom and into their careers.
“UT Knoxville’s engineering students are completing impactful research and development work that will ultimately define and attract future automotive partnerships,” said Uday Vaidya, IACMI-The Composites Institute chief technology officer and joint UT-Oak Ridge National Laboratory Governor’s Chair for Advanced Composites Manufacturing.
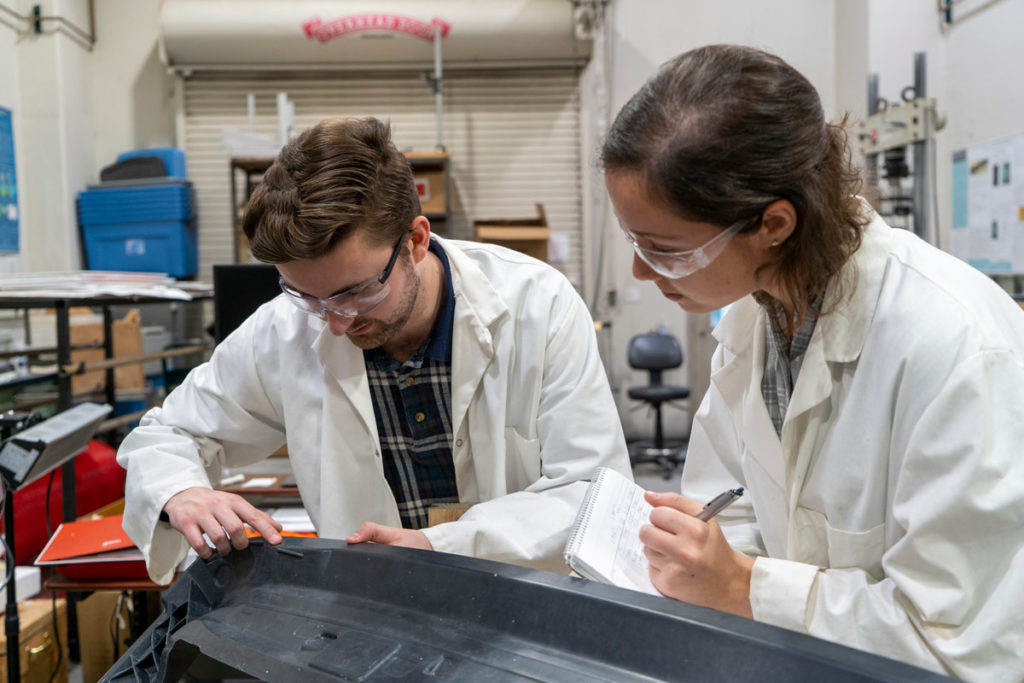
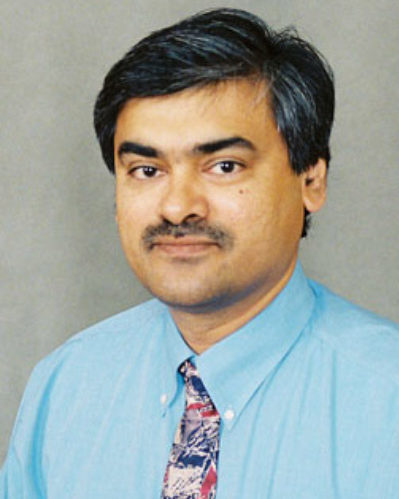
A win for the environment. A win for the car manufacturer. A win for UT Knoxville’s students.
By helping companies find answers to their questions, UT impacts industry near and far.